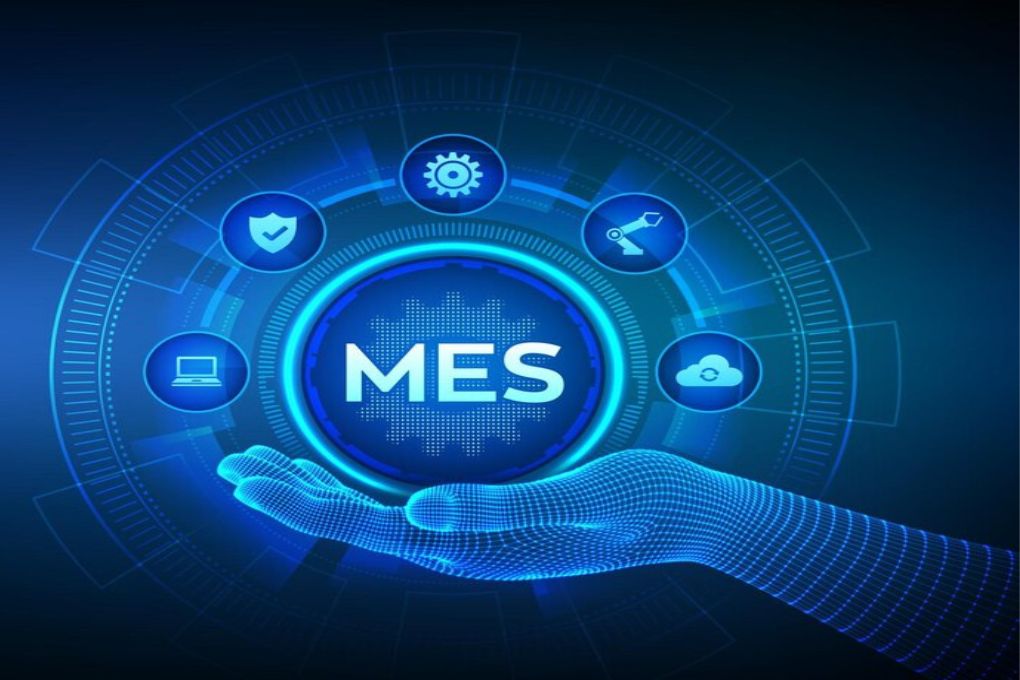
Every industrialist seeks to improve their productivity. How can we produce more faster while limiting the resources involved? Many methods and tools can contribute to this. Many are known and, fortunately, used. However, it is essential to regularly rethink new means that could make the production tool even more profitable. Among other things, the deployment of an MES * in the factory, in addition to the ERP, is most of the time particularly relevant. But how would the use of a solution of this type within your production units significantly increase the productivity of your company?
Gaining productivity is a way to improve the performance of your production tool. In fact, these gains make it possible to face the challenges that the company must respond to. Generating higher margins, simply developing, resisting a crisis, or even gaining market share are examples of this. Therefore, before implementing specialized software such as MES, it is essential to think about potential areas for internal improvement.
What first measures should be taken to increase industrial productivity?
We have said it: Before you want to install MES software, it is best to start by thinking about the simplest ways to influence productivity, make the most pragmatic arrangements, and act directly on what is already in place.
As a result, different stages can be identified. All of them make it possible to make the production tool more efficient or to gain profitability points:
Investment and qualification of teams
Promote the efficiency of employees regardless of their place within the production circuits. To this end, we can act on two levers. First, put in place regular training plans that will accelerate everyone’s skills development. Thus, better qualifications of employees will necessarily influence overall performance. Then, it is also necessary to improve working conditions to encourage their desire and, beyond that, their investment and loyalty. We will then limit staff turnover and reduce related costs.
Maintenance of the machine park
Guarantee the optimum condition of production through the implementation of maintenance processes. Monitoring and maintaining the machine fleet makes it possible to:
- Reduce the rate of equipment unavailability,
- Optimize their lifespan,
- Ensure the maximum quality of the products manufactured.
Relevant indicators
Implement monitoring tools. The machines only sometimes operate at total capacity. Consequently, measuring and monitoring their availability or usage rate using carefully chosen indicators is necessary to improve the performance of the entire productive tool.
Improved quality
Limit the rate of non-compliance. In-depth work on the means to put in place to reduce waste is a source of substantial savings. It makes it possible to minimize the costs linked to these non-compliant parts: time spent, waste of raw materials, storage, transport, etc.
Better communication
Communicate better within your production chains. Better communication is often a guarantee of quality, even when we are talking about manufacturing. It can take different forms, and in particular, that of automated communication, what we call workflows. In fact, it helps to reduce manufacturing times and minimize the number of errors.
Why would MES software contribute to better productivity?
The main advantage of Manufacturing Executive Systems (MES) software is to monitor your productivity in real-time. To do this, different means are at your disposal: Monitoring the OEE ( Synthetic Yield Rate ) of your workshop, visual management, and preventive maintenance of instruments.
- Monitoring the OEE: this machine utilization rate allows a simplified, transparent, and real-time view of the performance of equipment and production processes.
- Visual management: it is used to improve communication in your workshop. This tool is essential for the proper functioning of the production team relationship. It will highlight the state of live production, the objectives to be achieved, and the corrections to be made.
- Preventive maintenance of instruments: it aims to ensure production by analyzing and monitoring your industrial equipment. This way, you can guarantee continuous production with always optimal quality. The MES software manages all of your tools by identifying and listing your equipment, managing your stocks and purchases, planning interventions, managing a maintenance budget, and being able to analyze and decide for the good of your business.
Also Read : Common Challenges In ERP Implementation And How To Overcome Them