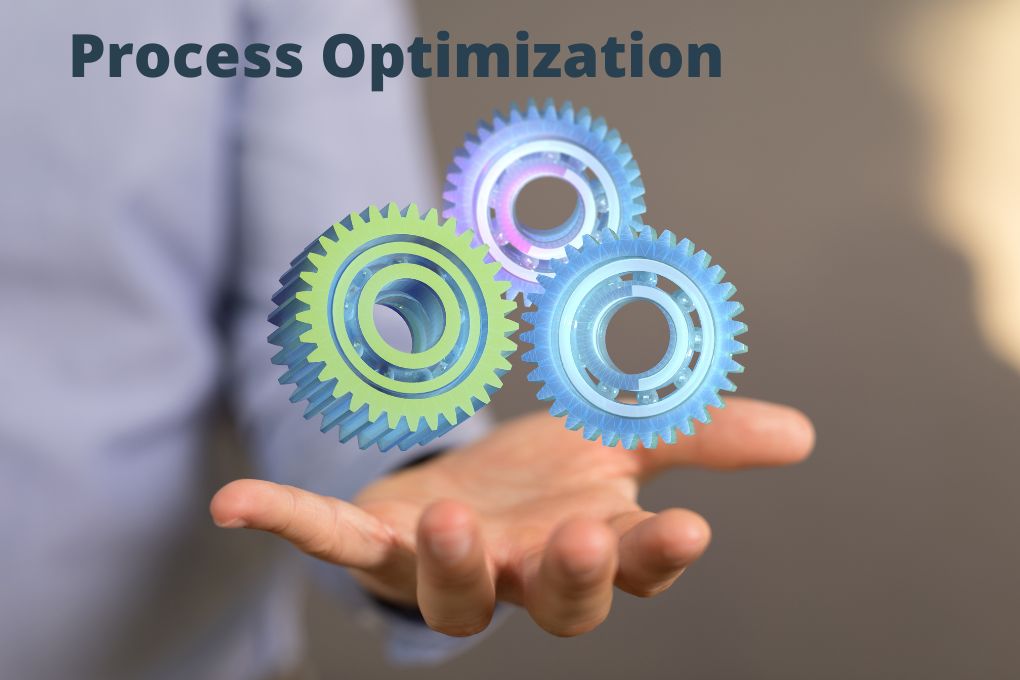
Continuously optimizing processes is a key task for companies to remain competitive in the 21st century!
What is process optimization? How does it work, what does it do and who optimizes processes? You will find answers to these questions in this post.
Definition: What is process optimization?
” Process optimization” means the intention to improve the effectiveness and efficiency of processes within companies in a targeted manner . In order to achieve this improvement, certain methods are applied and reasonable measures are taken .
Since the effectiveness and efficiency of processes always have to be considered in connection with current framework conditions, process optimization is an ongoing process that is never completed. The advancing digitization of certain sectors is currently playing a major role .
How does process optimization work?
analysis
In order to be able to optimize processes, they must first be analyzed. The current status must be surveyed . It is about the analysis of processes, products and services in order to uncover their weaknesses and potential. The length of the analysis varies depending on the scope.
redesign
Measures must then be developed in order to further expand the uncovered potential and to improve the weak points. This is often referred to as redesign . Of course, not all aspects can be tackled simultaneously and immediately. Nevertheless, it is important to think holistically and procedurally in this phase.
implementation
The developed measures form the basis for the implementation of the process optimization . The duration of the implementation phase depends on the scope of the agreed measures. At the beginning of the optimization of processes, individual measures such as the use of new software are often carried out.
What else belongs to process optimization?
After the analysis phase, the development of measures and their implementation, the optimization process should be evaluated. This means that the process itself should be subjected to an analysis.
evaluation
Within the evaluation , not only the success of the implementation should be considered. It is also important to evaluate which difficulties and positive starting points resulted from the analysis and the redesign. In this way, these findings can be included in further optimization of processes.
Leading questions can be, for example, the following:
- Which analysis methods were particularly positive for our team/our company and why?
- Which management concepts did not work and which could be used instead in the future?
- Where do we need help from external partners for further process optimization?
What methods of process optimization are there?
There are various methods that have to be selected depending on the industry and application. Basically, it is important that these methods are combined in a meaningful way.
The different methods for process optimization can be roughly divided into the following main categories :
- creativity techniques
- Analytical Methods
- More methods
We will present some of these methods below before showing the effects of process optimization.
creativity techniques
Creativity techniques can be used to analyze processes and generate ideas . There are a large number of creativity techniques that are often used in the following ways:
- brainstorming
- mind map
- 635 method
brainstorming
The best-known method is probably brainstorming. However, this method is often not that easy to implement. Brainstorming is about bringing in all ideas on a topic in a targeted manner, regardless of whether they initially appear realistic or feasible.
This is where visions are created, which often provide approaches for further thinking and, modified, lead to positive innovations. This often results in new food for thought. This can result in the depiction of a topic from different and holistic perspectives.
When brainstorming, it makes sense to involve people with different expertise in order to benefit from diverse perspectives. It makes sense to appoint moderators to collect the ideas.
mind map
A mind map can be created from the collected approaches of a brainstorming. However, it can also arise independently of this.
Mind maps focus on a central topic using a keyword or a short phrase. Based on this, sub -topics are then formed, which structure a topic by means of further branches. In contrast to brainstorming, the topic is already structured here. From this, requirements, responsibilities or implementation options can be derived.
635 method
6 people take part in a process analysis based on the 635 method , each writing down 3 ideas and passing them on to the other people 5 times. All participants then note down 3 more ideas and pass them on 5 times. In this way, many approaches to a subject area emerge within a very short time.
Creativity techniques offer an appreciative, motivating and promising approach , especially for companies that have so far relied less on employees participation.
Analytical Methods
Examples of analytical methods are “FMEA”, “cause-effect diagram” and “morphological box”.
FMEA
The abbreviation FMEA stands for Failure Mode and Effects Analysis. The aim is to uncover and record the possibilities for mistakes. Possible errors, error types, error causes, avoidance measures, detection measures and the risk priority number (RPN) are formulated in a table. They are intended to rank the risks.
Cause and Effect Diagram
The cause-and-effect diagram ( Ishikawa diagram ) contains a statement of a goal or problem, which is noted on the right side of a piece of paper. Possible solutions or possible causes of problems are formulated on the left by means of an arrow pointing to it.
Morphological box
Attributes and characteristics are compared in a table using the morphological box . Through the combination, different new solutions can be developed .
More methods
In addition to the “creativity techniques” and “analytical methods” mentioned above, there is a multitude of management concepts .
The methods presented here go beyond the analysis process and support the redesign and implementation.
5S method
The 5S method refers to the process of work design and aims at the organization of the workplace. It describes a procedure for sorting, ordering, cleaning, considering and maintaining this state as a standard. It often forms the basis for further optimization measures.
Six Sigma
Six Sigma is often used in industries such as the automotive industry. Six Sigma defines a statistical quality goal , which is why it is mostly used in quality management to drive process improvements.
For example, the “DMAIC” cycle (Define, Measure, Analyze, Improve, Control) is used. This is a standardized procedure that is intended to enable targeted and controlled process optimization.
What does process optimization do?
There is neither one method nor one effect of process optimization. Like the choice and combination of methods, the effect of process optimization also depends on various factors.
Different industries, company sizes and objectives influence the effects of process optimization. 7 effects that are often to be achieved are shown below as examples.
1. Productivity increase
Increased productivity is certainly a goal that process optimization often pursues. It can be achieved in a number of ways. As a rule, a combination of technical and organizational means is used.
2. Quality improvement
Improving the quality of products is often a central concern in efforts to optimize processes. It doesn’t matter whether it’s a physical product, software or service.
Rather, it is about selecting suitable measuring and testing equipment that can demonstrate a possible improvement in quality. Statistical processes such as Six Sigma or the other approaches described above are considered quality assurance methods.
3. Shortening of throughput times
The lead time is the period of time required from the beginning to the completion of a work process. When reporting a claim in the insurance industry, this includes reporting the claim, processing and settlement.
Shortening throughput time plays a major role because it reduces costs if the resources saved can be used elsewhere.
Examples of questions that can be asked in the lead time reduction analysis are:
- Where are longer waiting times?
- How do they arise?
- How could that be changed?
4. Reduction of resources
Resource reduction or conservation is a central topic in companies. Buzzwords in this context are “sustainability” and “efficiency” , but increasingly also “work-life balance”.
As part of process optimization, automation is increasingly being used to improve human resources . In this way, human resources can be used where their individual experience, knowledge, opinions, ideas or social skills are required.
5. Improvement of processes
In order to be able to improve processes, weak points and potential for improvement must be uncovered using analysis techniques. Measures can then be developed and implemented.
A process that can be significantly simplified and optimized through digitization is, for example, the signing of contracts . Contracts must be forwarded to customers for signature. This is often done either by post, via e-mail or as a download. Customers then have to sign the paper documents by hand and either scan them or send them back by post.
All this costs time, money and is cumbersome. This process also results in longer throughput times.
6. Improving communication
Modern information and communication technology is becoming increasingly important in everyday business. Communication affects different areas from industry to industry. In principle, communication between employees or with customers can be optimized.
Improving communication processes can involve the technical implementation of communication, communication content or the communication culture.
Use the analysis methods presented here as well to highlight which areas of communication within your company should be optimized.
Good video conference systems and groupware software, for example, are important technical implementation tools for communication between employees .
Also Read : Digital Signature For Companies